Technology | Application analysis of metal fiber filter in the field of cement dust removal
Time:
2020-10-16
1. Current status of dust removal in the cement industry
With the rapid development of my country's economy, cement has played an increasingly important role in the national economy, especially during the "Eleventh Five-Year Plan" and "Twelfth Five-Year Plan" period, my country's cement industry has achieved rapid development. my country’s current cement plants generally use dry process, and the new dry process cement technology has made breakthroughs in energy saving and large-scale. As of the end of 2017, a total of 1715 new dry process cement production lines nationwide have been removed or removed in 2016. Unrecoverable production line), the designed clinker production capacity reached 1.82 billion tons, and the actual annual clinker production capacity still exceeded 2 billion tons. At present, the scale of the new dry-process cement kiln is mainly based on the clinker scale of 5000t/d, and the scale has reached 12,000t/d. material.
Among the main emission sources of industrial dust, the dust produced by the cement industry accounts for about 70% of the total emissions, which has seriously polluted the environment. The newly revised "Cement Industry Air Pollutant Emission Standards" (GB4915-2013) was released in 2013. Released on December 27th. In order to meet the needs of the country’s "13th Five-Year Plan" and environmental management for a period of time in the future, and to effectively strengthen the emission control of particulate matter, SO₂, NOX, etc., the Ministry of Environmental Protection recently issued the The Announcement of Emission Limits, decided to implement special emission limits for air pollutants in Beijing-Tianjin-Hebei air pollution transmission channels.
Specifically to the cement industry: new construction projects that accept environmental impact assessments will implement special emission limits for air pollutants from March 1, 2018; if there are stricter emission control requirements in the localities, they will be implemented according to local requirements. Existing companies have implemented special emission limits for sulfur dioxide, nitrogen oxides, particulate matter, and volatile organic compounds from October 1, 2018. According to the released emission limit data: the emission limit of thermal equipment such as cement kiln and kiln tail waste heat utilization system, dryer, drying mill, coal mill and cooler is 30mg/Nm³, crusher, mill, packaging machine The emission limit of ventilation equipment is 20mg/Nm³. In addition, enterprises in key areas implement special emission limits for air pollutants: the emission limit for thermal equipment is 20mg/Nm³, and the emission limit for ventilation equipment is 10mg/Nm³. Some even implement the transformation according to the emission standard of 5mg/Nm³.
In the process flow of the new dry-process cement production line, the largest dust pollution source in cement plants is mainly concentrated in the dust emissions from the kiln head and kiln tail. According to the new standard (GB 4915-2013), the emission limit requirements of the kiln head and Only by adopting a high-efficiency electric one-bag composite dust collector at the kiln end, using the coarse filtration of the electric dust collector and the high-precision filtration of the bag filter material, can ultra-low emissions be achieved. Because the bag filter has the advantages of processing fine dust, high dust removal efficiency, simple structure, strong adaptability, and stable system operation, under the application of the new standard emission requirements, the bag filter has more advantages than other dust removal methods.
2. Existing problems and improvement methods
According to the current cement production technology, it can be divided into two types: power generation with waste heat and power generation without waste heat. Under the condition that the existing technology remains unchanged, the temperature of flue gas entering the dust collector from the cement kiln tail when power generation with waste heat is 130-150℃. The temperature of the air entering the kiln head dust collector is 80-100 ℃; when the power generation without waste heat, the temperature of the flue gas entering the dust collector from the cement kiln tail is 130~150 ℃ (instantaneously up to 200 ℃ or more), The air temperature is 250~380℃ (Electric precipitator, if the kiln head is a bag precipitator, a heat exchanger must be added before the precipitator).
At present, most of the bag filter bag materials are aramid, polyimide, PPs, PTFE, etc., and the maximum temperature resistance does not exceed 280℃. When the temperature in the kiln fluctuates (mainly at the kiln head), bag burning is easy to occur. Bag-gluing accidents have broken bags, causing excessive emissions and higher operating costs. With the continuous deepening of filter material research technology, a batch of materials with high temperature resistance, corrosion resistance and high filtration accuracy, such as metal fiber sintered felt, intermetallic compound powder filter material, ceramics and other metal and inorganic materials, have broken the original filter The limitation of material temperature resistance can be applied to the transformation of the kiln head dust collector (applicable to the electric precipitator reconstruction project without waste heat power generation).
3. Features of metal fiber filter media
The metal fiber felt is a porous depth filter material that is made of metal fibers with different wire diameters (1-100μm) and is sintered at a high temperature by a non-woven paving method. The thickness is between 0.4 and 1mm. The finished product and micro The structure is shown in 1. The metal fiber felt is mainly made of stainless steel with high temperature resistance and corrosion resistance, such as 304, 316L, 310s, etc. The recommended operating temperature is 600℃, while the use temperature of FecrAl metal fiber felt can reach 1,000℃. Because the fiber diameter is in the micron level and all are through holes, the porosity of the fiber mat is over 80%, which is much higher than other high temperature resistant filter materials, such as metal powder and ceramic filter materials.
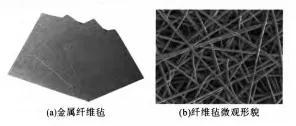
The initial resistance of the metal fiber filter material is only 30-100Pa, and the curved channel inside the filter material can block and absorb a large number of pollutants of different shapes and particle sizes, so its dirt holding capacity is much higher than other filter materials. The metal fiber filter bag does not generate static electricity during the filtration process, and will not adsorb dust. The surface of the metal fiber is smoother than that of a cloth bag, and the dust is easy to fall off during the blowback process. The filter bag can be recycled. When a serious blockage occurs, it can be reused with high-pressure water or air flushing. Once the cloth bag is blocked, it can only be replaced; its filtering performance is stable. Through high temperature sintering, the aperture will not deform under high pressure and cause leakage. When the bag is blocked, dust will penetrate and the emission will exceed the standard.
The good match of toughness and thermal conductivity of the porous metal filter material makes its shock resistance and heat resistance better than ceramics, and is not prone to fracture. The metal material can be subjected to secondary processing such as welding and bending, which is convenient for packaging with the overall system. For example, the corrugated metal filter material method is used to increase the filter area and save the floor space. The ceramic filter element and powder filter material are rigid materials, which are prone to brittle cracks during installation and use, and replacement is troublesome. Metal fiber felt has good toughness and can be used. Withstanding bending deformation, it has better applicability and superiority in the application of high temperature dust removal filter media.
4. Comparison of performance characteristics of different filter media
4.1 Comparison of filtration performance stability of different filter media
At present, some cloth bag manufacturers claim that their filter material can intercept 2μm dust, but the actual situation is that as the pressure of the bag filter increases, the fibers in the bag filter material deform, which makes the pore size increase. Three kinds of filter media with a filtration accuracy of 2μm are calibrated as gas-solid and their filtration accuracy is measured by bubble point method. As shown in Table 1: The bubble point of the flexible filter material (PTFE or PPS) is lower than that of the metal fiber felt, and the corresponding interception particle size is much higher than 2μm. Therefore, in actual use, under the dual effects of operating temperature and filtration pressure, the pore size of the bag filter material will increase, which will inevitably affect the filtration accuracy and cause the emission to exceed the standard. The metal fiber filter material is sintered at high temperature, and the fibers are firmly welded through diffusion. Under normal filter pressure, there will be no problems similar to the substandard discharge of cloth bags. The unique high porosity of the metal fiber filter material makes it The air permeability is much higher than the other two materials.
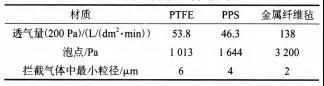
4.2 VDI test of filtration performance of different filter media
The metal fiber filter material and the commonly used film-coated PTFE filter material in the market are tested for the performance comparison of filtration VDI. The test standard is "Technical Requirements for Bag Filters" (GB/T 6719-2009), and the test dust is alumina standard dust. The concentration is 5g/m³, and the results are shown in Table 2. It can be seen that the resistance of the metal fiber filter (1μm) in the clean state is only 38 Pa, which is much lower than the initial resistance of the membrane filter, and the initial filtration efficiency can reach 99.98%. When the metal filter material ages, its filtration efficiency is basically the same as that of the coated filter material, and the resistance of the filter material is stable below 500Pa. Compared with the traditional coated PTFE filter material, the filter effect of "high efficiency and low resistance" is truly realized.
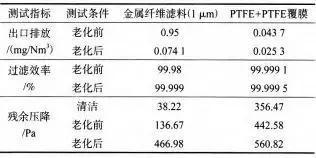
5. Filtering mechanism and application of metal fiber filter media
5.1 Filtration mechanism of metal fiber filter media
At present, with the continuous improvement and breakthrough of superfine fiber technology, the diameter of the metal fiber prepared by the technical drawing method can be as thin as 1μm, and the gas-solid filtration accuracy of the fiber mat prepared by it can reach 0.2μm. In the design of the filter material, ultrafine fibers are used as the windward side of the metal fiber felt filter material, combined with the use of fibers with a larger diameter as the support layer, to form a structure with a gradient structure pore size from small to large on the surface of the filter material (see figure 2) The fine fiber layer prevents most of the dust from staying on the surface of the filter material, and plays a role of surface filtering. In this way, it is not necessary to rely solely on the filtering effect of the dust layer, nor does too much dust enter the deep layer of the filter material, which increases the running resistance. The fiber layer can enhance the strength of the filter material, increase the impact resistance to the airflow, reduce the pressure drop, and the pulse back-blowing effect is good, the air consumption is small, and the energy consumption is reduced.
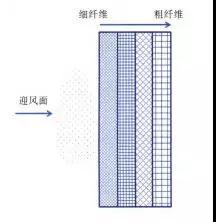
The metal fiber filter bag used as an industrial dust collector is made by cutting, rolling and welding metal fiber filter material. The inside of the filter cartridge is supported by a stainless steel frame to increase its compressive strength. Generally, the main diameter of the filter bag is ∅130mm, ∅160mm, and the length ranges from 1 to 8m. When installing, the bag mouth is sealed with flanges, high temperature gaskets and pressure blocks. The metal fiber filter bag and on-site installation are shown in Figure 3.
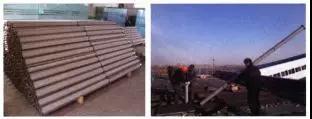
The company uses metal fiber filter bags to filter the high-temperature gas containing gaseous rhenium and then cool it down, successfully realizing the recovery of rhenium metal. In the calcination process of the titanium dioxide rotary kiln, the high-temperature flue gas (the temperature is about 450℃) produced is directly filtered through the metal filter bag. On the one hand, it can effectively prevent environmental pollution, and more importantly, the filtered high-temperature gas can be returned to the kiln. Reheat, successfully realize waste heat utilization. Taking 20000m³/h of high-temperature flue gas as an example, through the use of waste heat, more than 10,000 yuan of energy can be saved every day.
In May 2017, the company conducted a high-temperature dust removal test in front of the kiln head of a dry-process cement production line of a cement plant in Shaanxi for the first time. A high-temperature induced draft fan was used to draw 6000m³/h of flue gas from the main pipe at a temperature of 280-320℃ and passed through a metal fiber filter bag. Perform high-temperature filtration. Among them, the design filter wind speed is 1~1.2m/min, the ash cleaning pressure is 0.3~0.4MPa by using timing cleaning and online pulse cleaning. The initial operating resistance of the equipment is about 350Pa. After 3 months of non-stop operation, the weighing method was used to detect the dust concentration of the inlet and outlet pipes of the dust collector. The inlet concentration was 48.3g/Nm³, the outlet concentration was 5.62mg/Nm³, the dust removal efficiency reached 99.98%, and the operation resistance remained at 800~1000Pa.
6. Summary
In short, traditional filter materials such as cloth bags have a short service life above 260°C. Ceramic and metal powder filter materials have advantages over traditional filter materials in terms of filtration efficiency, stability and high temperature resistance, but the biggest problem is that the whole is very brittle. Easy to break, high filtration resistance, poor cleaning effect, high operation and maintenance cost. The unique strength and toughness, high temperature resistance, corrosion resistance, and easy processing and forming capabilities of metal fiber filter materials will definitely become the first choice for high temperature dust removal filter materials. The emission indicators after filtration with metal filter bags fully meet the requirements of national ultra-low emission standards. . The metal fiber filter material will surely occupy an important position in the high temperature flue gas dust removal industry and win a broad market. Research and development on it will bring huge social, economic and environmental benefits to the country.