Characteristics and application of metal fiber sintered felt
Time:
2020-06-24
1. Production process and characteristics of metal fiber sintered felt
Metal fiber sintered felt is a bundle of multi-metal wires, stretched to a usable fiber diameter at the same time, and then used the same weight and standard diameter to bundle them into filaments, cut them, and use a suitable method to make a fluffy felt. A variety of fluffy felts with different diameters are arranged together in order to form a certain thickness of stacked fibers, so that the fibers cross each other to form gaps, and then sintered and rolled into a finished sintered felt.
Metal fiber sintered felt is a bundle of multi-metal wires, stretched to a usable fiber diameter at the same time, and then used the same weight and standard diameter to bundle them into filaments, cut them, and use a suitable method to make a fluffy felt. A variety of fluffy felts with different diameters are arranged together in order to form a certain thickness of stacked fibers, so that the fibers cross each other to form gaps, and then sintered and rolled into a finished sintered felt.
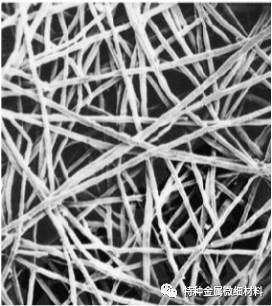
The metal fiber sintered felt has a very fine stainless steel fiber structure, which is laid and compacted in a three-dimensional labyrinth pattern, has many intersections, and has a high barrier capacity. This material has at least two layers of fiber structures with different diameters, so it can be obtained More than two levels of filtration capacity. To
Due to the combination of high length and diameter of metal fiber used in the sintering process, the metal fiber felt can weld countless contact points of the fiber together. Therefore, this material has no medium transfer, good strength, good air permeability, and circulation. The resistance is small. To
The metal fiber felt uses special metal fibers (stainless steel, iron, chromium, aluminum, etc.), so it has high mechanical strength and toughness under high temperature conditions. To
Metal fiber sintered felt has an excellent filtering effect on polyester condensate that is not easy to filter and easily deformable colloid, and it has a wide range of applications in the chemical industry, chemical fiber and other fields.
Due to the combination of high length and diameter of metal fiber used in the sintering process, the metal fiber felt can weld countless contact points of the fiber together. Therefore, this material has no medium transfer, good strength, good air permeability, and circulation. The resistance is small. To
The metal fiber felt uses special metal fibers (stainless steel, iron, chromium, aluminum, etc.), so it has high mechanical strength and toughness under high temperature conditions. To
Metal fiber sintered felt has an excellent filtering effect on polyester condensate that is not easy to filter and easily deformable colloid, and it has a wide range of applications in the chemical industry, chemical fiber and other fields.
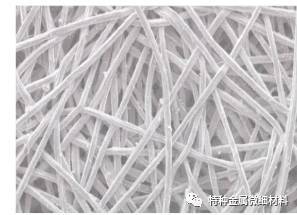
Compared with other filter materials, metal fiber sintered felt can block colloidal substances even at very high temperatures. The reason is that the thin metal wires have many contact points, which have a strong blocking ability. This filter material has at least It is composed of two layers of metal felt, which can form a three-dimensional gradient filter, so this material has a high dirt holding capacity. Compared with the metal woven mesh, it has 3 to 4 times the dirt holding capacity and 2 to 3 times the air permeability. The degree is 21 to 600 times that of the powder sintered filter element, and the filtration efficiency is 3 to 15 times that of the metal woven mesh. To
The sintered wire felt can have different characteristics according to its structure and shape. Among them, the folded cylindrical type has a large filtering area, strong penetration and easy installation; the slender tubular shape is easy to clean, and the flow resistance is small. The disadvantage is that the dirt holding capacity is small, and the concentric circle It can be made into a frameless filter element, which saves costs, but it is inconvenient to load, unload and clean. To
2. Filtration process of metal fiber sintered felt
Metal fiber sintered felt filter material has two stages in the fluid filtration process:
The first stage (ie stable stage):
The filter material of metal fiber sintered felt filter is originally clean, and its material structure and shape are fixed. In the initial stage of filtration, when the dust-containing fluid passes through the pore channels of the filter material, under the combined action of various filtration mechanisms, the fluid containing pollutant particles will quickly disperse, fill up the various channels of the filter material, and accumulate in it. Pore surface or filter material surface. As the seepage continues, the liquid flow mainly moves along the normal channel. At this time, the resistance of the filter material is relatively stable. This stage is actually short-lived and will end soon. To
The second stage (i.e. unstable stage):
As the pores of the filter material become narrower and narrower, and even gradually become clogged, contaminant particles accumulate on the surface of the filter material to form a filter cake and form a new filter layer. This process is the main working condition of the filter material. In this state, the pollutant particles in the system must be simultaneously filtered by the filter cake and the filter material. At this time, the resistance of the filter material continues to rise, and the filtering effect is in an unstable state. The filtration efficiency is much higher than that of the filter cake on the surface of the filter material. The relationship of its filtration efficiency is: η filter cake formation after η filter cake formation> η cleaning filter material.
3. Cleaning of metal fiber sintered felt
As a filter medium that can be cleaned, the metal fiber sintered felt has a long service life, and its production cost is higher than that of other disposable filter materials. Due to the environmental and cost considerations, the periodic or Irregular maintenance is also very necessary. To
Principles and methods of chemical cleaning:
The most common chemical cleaning method is the acid-base cleaning solution cleaning method, which is the most effective method for collecting polyester coagulation filters by using acid-base solutions during chemical cleaning. To
Ultrasonic cleaning method:
Ultrasound is a wave energy that continuously pressurizes and expands. This energy can generate air pockets when applied to the liquid, and the continuously broken air pockets can have a cleaning effect on the sintered felt. To
heat treatment cleaning:
Vacuum pyrolysis, heating oven, liquefied bed and hot salt bath are all methods of cleaning sintered felt. They are commonly used when chemical cleaning methods are not effective. To
Note: After cleaning the sintered felt filter element, a bubble point test must be performed to check its integrity and measure the pressure drop of the filter element. To
4. Parameters of metal fiber sintered felt:
The sintered wire felt can have different characteristics according to its structure and shape. Among them, the folded cylindrical type has a large filtering area, strong penetration and easy installation; the slender tubular shape is easy to clean, and the flow resistance is small. The disadvantage is that the dirt holding capacity is small, and the concentric circle It can be made into a frameless filter element, which saves costs, but it is inconvenient to load, unload and clean. To
2. Filtration process of metal fiber sintered felt
Metal fiber sintered felt filter material has two stages in the fluid filtration process:
The first stage (ie stable stage):
The filter material of metal fiber sintered felt filter is originally clean, and its material structure and shape are fixed. In the initial stage of filtration, when the dust-containing fluid passes through the pore channels of the filter material, under the combined action of various filtration mechanisms, the fluid containing pollutant particles will quickly disperse, fill up the various channels of the filter material, and accumulate in it. Pore surface or filter material surface. As the seepage continues, the liquid flow mainly moves along the normal channel. At this time, the resistance of the filter material is relatively stable. This stage is actually short-lived and will end soon. To
The second stage (i.e. unstable stage):
As the pores of the filter material become narrower and narrower, and even gradually become clogged, contaminant particles accumulate on the surface of the filter material to form a filter cake and form a new filter layer. This process is the main working condition of the filter material. In this state, the pollutant particles in the system must be simultaneously filtered by the filter cake and the filter material. At this time, the resistance of the filter material continues to rise, and the filtering effect is in an unstable state. The filtration efficiency is much higher than that of the filter cake on the surface of the filter material. The relationship of its filtration efficiency is: η filter cake formation after η filter cake formation> η cleaning filter material.
3. Cleaning of metal fiber sintered felt
As a filter medium that can be cleaned, the metal fiber sintered felt has a long service life, and its production cost is higher than that of other disposable filter materials. Due to the environmental and cost considerations, the periodic or Irregular maintenance is also very necessary. To
Principles and methods of chemical cleaning:
The most common chemical cleaning method is the acid-base cleaning solution cleaning method, which is the most effective method for collecting polyester coagulation filters by using acid-base solutions during chemical cleaning. To
Ultrasonic cleaning method:
Ultrasound is a wave energy that continuously pressurizes and expands. This energy can generate air pockets when applied to the liquid, and the continuously broken air pockets can have a cleaning effect on the sintered felt. To
heat treatment cleaning:
Vacuum pyrolysis, heating oven, liquefied bed and hot salt bath are all methods of cleaning sintered felt. They are commonly used when chemical cleaning methods are not effective. To
Note: After cleaning the sintered felt filter element, a bubble point test must be performed to check its integrity and measure the pressure drop of the filter element. To
4. Parameters of metal fiber sintered felt:
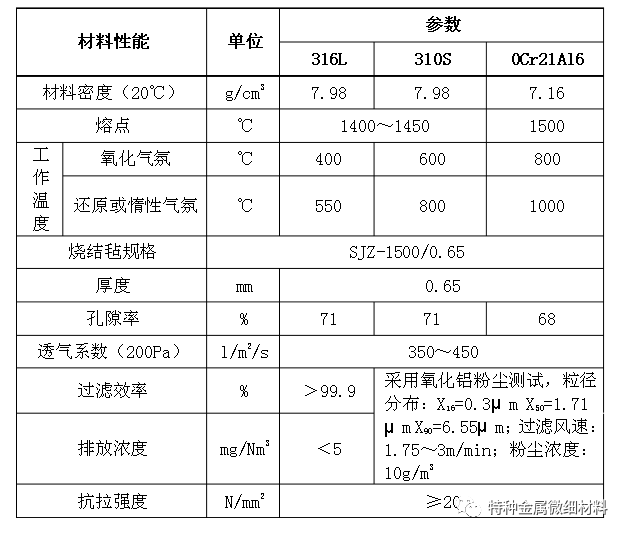
5. Features of metal fiber sintered filter felt:
1) High porosity and excellent permeability, low pressure loss, large flow; 2) Large dirt holding capacity, high filtration accuracy, slow pressure curve rise during use, and long replacement cycle;
3) Excellent temperature and corrosion resistance, long-term use at 600℃, nitric acid,
Corrosion of alkalis, organic solvents, and chemicals;
4) High strength, not easy to deform; can be folded to increase the filter area, and can be welded;
5) It can be cleaned and regenerated, even if the liquid is strongly washed or shaken, the fibers will not fall off;
6) Can be used multiple times. To
6. The main purpose of metal fiber sintered filter felt:
1) Chemical fiber and film industry: filtration and purification of polyester, nylon, polyester and other polymer melts, making melt filter elements and textile filter layers;
2) Filtration and dust removal of various high temperature and corrosive gases in the petroleum, chemical and metallurgical fields; 3) Filtration of various high temperature and corrosive liquids in the petroleum and chemical industries;
4) Precision filtration of hydraulic oil and lubricating oil in the fields of machinery, shipbuilding, electric power, electronics, aviation, aerospace, etc.;
5) Clarification and filtration of various liquids in the pharmaceutical, biological, and beverage industries. To
Seven, metal fiber sintered filter cartridge
At present, the filter cartridges on the domestic market basically use polyester fiber as the base material. Due to its low temperature resistance, the temperature of the conventional filter cartridge is below 135℃, which determines the high temperature conditions of the filter cartridge. Limitations of the application. Based on many years of engineering experience, our company independently developed a high temperature resistant filter cartridge according to market demand. Its use temperature can reach 350℃, which even exceeds the use conditions of high temperature resistant cloth bags (use temperature of 260℃). It marks that the application range of the filter cartridge has improved a step.
1) High porosity and excellent permeability, low pressure loss, large flow; 2) Large dirt holding capacity, high filtration accuracy, slow pressure curve rise during use, and long replacement cycle;
3) Excellent temperature and corrosion resistance, long-term use at 600℃, nitric acid,
Corrosion of alkalis, organic solvents, and chemicals;
4) High strength, not easy to deform; can be folded to increase the filter area, and can be welded;
5) It can be cleaned and regenerated, even if the liquid is strongly washed or shaken, the fibers will not fall off;
6) Can be used multiple times. To
6. The main purpose of metal fiber sintered filter felt:
1) Chemical fiber and film industry: filtration and purification of polyester, nylon, polyester and other polymer melts, making melt filter elements and textile filter layers;
2) Filtration and dust removal of various high temperature and corrosive gases in the petroleum, chemical and metallurgical fields; 3) Filtration of various high temperature and corrosive liquids in the petroleum and chemical industries;
4) Precision filtration of hydraulic oil and lubricating oil in the fields of machinery, shipbuilding, electric power, electronics, aviation, aerospace, etc.;
5) Clarification and filtration of various liquids in the pharmaceutical, biological, and beverage industries. To
Seven, metal fiber sintered filter cartridge
At present, the filter cartridges on the domestic market basically use polyester fiber as the base material. Due to its low temperature resistance, the temperature of the conventional filter cartridge is below 135℃, which determines the high temperature conditions of the filter cartridge. Limitations of the application. Based on many years of engineering experience, our company independently developed a high temperature resistant filter cartridge according to market demand. Its use temperature can reach 350℃, which even exceeds the use conditions of high temperature resistant cloth bags (use temperature of 260℃). It marks that the application range of the filter cartridge has improved a step.
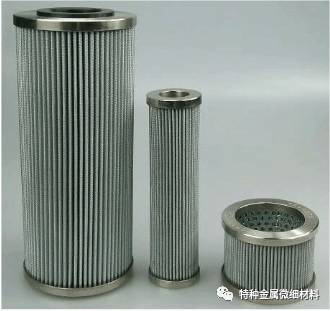
Features:
1) The base material is made of multilayer high-performance metal wire drawing and sintering;
2) It is resistant to acid and alkali corrosion, and the temperature can reach 350℃;
3) It has good air permeability and low running resistance;
4) The substrate has good electrical conductivity and anti-static properties;
5) It is suitable for harsh working conditions with high flue gas temperature, acid and alkali corrosion, and high dust concentration.
1) The base material is made of multilayer high-performance metal wire drawing and sintering;
2) It is resistant to acid and alkali corrosion, and the temperature can reach 350℃;
3) It has good air permeability and low running resistance;
4) The substrate has good electrical conductivity and anti-static properties;
5) It is suitable for harsh working conditions with high flue gas temperature, acid and alkali corrosion, and high dust concentration.